依照某混凝土公司持续两年统计分析各磨机高铬球的耗费测算,生料为60 g/t,水泥粉磨为90 g/t,吨混凝土综合性(含煤磨球耗)为130 g/t,年产量400万t混凝土经营规模的混凝土公司,历年耗费轴承钢球350 t,再加鄂板、隔仓板、倒料篦板等磨机金属复合材料耗费达700 t,按当今高铬球价钱6 600元/ t测算,历年耗费金属复合材料费约400万余元,吨混凝土成本费约1元。
随之在我国混凝土工业生产经营规模的不断发展,混凝土加工过程中原材料的粉磨仍未保持无球化,一部分新式半干法窑粉磨生料、粉煤虽已应用立磨,但其他原材料粉磨包含水泥粉磨站等绝大多数仍应用各式各样的湿式球磨机开展粉磨,历年要耗费很多的碾磨体、隔仓板、鄂板等金属耐磨材料。
一、金属耐磨材料的发展趋势全过程
水泥粉磨常用金属耐磨材料大概亲身经历了3个环节:
第一个环节:要以高锰钢为意味着的金属复合材料,用在高冲击性、强损坏负荷标准下,如大中型鄂式破碎机颚板、大中型锤破高铬合金锤头等;
第二个环节:要以镍硬生铁为意味着的金属复合材料,世界各国迄今还要立磨的磨辊上运用,但因为其马氏体含水量高、延性大,稀有金属材料镍的添加量很大,产品成本高,其运用和营销推广遭受必须的限定;
第三环节:要以高铬铸铁和各种碳素钢为意味着的金属复合材料,如球磨机衬板、磨球、反击破碎机板锤等。高铬铸铁和碳素钢以非凡的性价比高替代了高锰钢。
以磨机鄂板为例。20世纪65时代均选用高锰钢,75时代后被碳素钢和高铬铸铁所替代。第三代金属复合材料各有特色,在不一样的负荷标准下获得运用。中锰钢以殉职延展性获得更高的冷作硬化工作能力,用以中等水平冲击性标准下的磨机鄂板、小高铬合金锤头。高铬铸铁有许多优势。
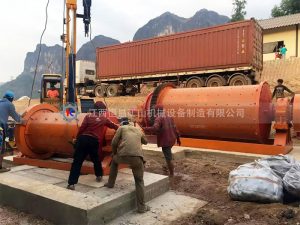
首位,在含铬13%时能够产生Fe7C3型马氏体,显微镜强度HV1300~2500,比一般白口铁中Fe3C型马氏体的显微镜强度HV800~1 150高许多,因而耐磨性能好;
其次,马氏体样子有所不同,呈断蜂窝状、屁股状,因而比蜂窝状马氏体延展性高;除此之外,高铬铸铁的常规能够根据不一样的热处理方法来得到从所有铁素体到所有奥氏体的各种各样常规以扩张其运用范畴。
在我国混凝土工业生产中的粉碎、粉磨机器设备很多年来始终选用高锰钢。高锰钢的特性是:延展性极高,在高冲击性负载的标准下可造成冷作硬化,进而主要表现出优质的耐磨性能,可是其抗拉强度低,应用极易造成塑性形变、拱凹等,且强度很低,在冲击性负载不足大的状况下,耐磨性能很差。因而在一般高锰钢基本上,发展趋势了铝合金高锰钢、中锰钢及超宽锰碳素钢。中锰钢用以中小磨磨机鄂板,比一般高锰钢提升使用寿命60%~90%。
20世纪90时代后低、中、高铬铸铁磨球、鄂板陆续资金投入运用。用高锰钢生产制造的隔仓板,延展性不错,不产生破裂,但冲击性时易出現形变,使篦缝变小。
如Φ3.2 m&am p;ti mes;6.3 m水泥磨,隔仓板在损坏过段时间后篦缝从13 mm铆至3mm~5 mm,每一次关机维修要开展去除,情况严重得用氧割开展吹割。
改成碳素钢鄂板后,篦板不产生形变,篦缝保持不变,磨内自然通风维持一切正常,但也是断掉状况。
二、存在的不足及解决方案:
因为混凝土经营规模的不断发展,在建水泥粉磨站也雨后春笋般,非常是某些非水泥行业小区业主在建水泥粉磨站,刚进到水泥行业,对水泥粉磨生产工艺较为欠缺,沒有专业技术人员,沒有工作经验,管理方法单一化,对碾磨体的管理方法与应用不合理,存有某些难题,导致水泥粉磨全过程中金属复合材料耗费提高,成本增加,在管理方法关键点上不细致,存有不一样材料的碾磨体互用,计量检定不精确,加碾磨体不立即,加量不测算,磨内配合比不可以维持有效的配合比,导致磨内持仓过高或过低,加工工艺操纵不科学。
1、研磨材料的互用
碾磨体做为水泥粉磨全过程中的碾磨物质,依据不一样的粉磨原材料,应取用不一样材料的碾磨体及有关金属复合材料。如今一部分中小型混凝土公司有效生铁球、低碳环保铝合金球、低铬球、高铬球,有的公司乃至自己生产加工生铁球。各种各样原材料的成份差别很大,耐磨性也区别很大。
相同材料的碾磨体,不一样的生产商因为碾磨体的制作工艺不一样,其工艺性能及应用实际效果也区别很大。但在应用全过程中,非常是中小企业管理不足严苛,出現不一样材料的碾磨体混和应用状况,尤其加碾磨体时,因为资产等层面的缘故,不按原材料的碾磨体购入,廉价购买与原先不一样材料的碾磨体,使表层强度、耐磨性不尽相同的几类碾磨体混和在相同磨机内应用。
如山东省ZL化工厂,有5台Φ3.2 m×6.3 m的生料机混凝土磨机,2008年因为资产艰难,公司出現短期行为作法,选用了很多的自炼磨球,虽价钱较低,但磨球特性拙劣。由于资产困惑,未能补入原用高铬球,一起也并不是将磨内碾磨体所有拆换,在原先用高铬球的基本上,所有补入自炼球,使高铬球与生铁球混和应用,其应用实际效果偏差。
每一次Ⅰ仓补入Φ150、Φ95、Φ90等大球,Ⅱ仓Φ60的球,应用一月之后,碾磨体损坏比较严重,持仓降低,添加Φ150的大球直徑过少150 mm,添加Φ95的大球直徑过少95 mm,过了2六个月后,只有作为Φ95、Φ90的球应用,导致磨内配合比错乱,不可以维持磨内有效的配合比。导致磨机台时生产量降低,耗费上升,热耗扩大(如表1),年提升成本费180万余元。
自炼铸铁价格只能5 0500元/t,那时候高铬球为7 0500元/t,可是自炼球是外企业应用我厂废金属生产加工,材料不一样,制作工艺不一样,碾磨体品质无法确保:表层强度不合格,言行不一,在应用全过程中不耐磨损,碾磨体损坏快;锻造全过程中球内有沙眼。不一样材料的自炼球与高铬球在相同仓内互用,磨球表层与內部特性不同,內部出現凹壳、失圆,一起出現较多的裂开,导致碾磨体耗损大;一起,生铁球与高铬球在相同仓内相互应用,出現硬吃软状况,低强度的碾磨体损坏快,导致水泥粉磨球耗上升。只此这项,年产量40万t混凝土成本费则升高181.5万余元。
2、碾磨体与鄂板、篦板等不配对
水泥磨、生料磨的金属复合材料包含碾磨体、鄂板、隔仓板、篦板等,在应用全过程中,应严苛配套设施。有的公司却不留意,刚建成投产时按新设计方案的计划方案开展拼装,材料大部分相符合,即球与鄂板、隔仓板篦板等特性相一致,但在之后的维修加球全过程和购置碾磨体时考虑到价钱要素,沒有从材料上开展配对,如磨内的高铬球改成加一般球,或将隔仓板Mn13改成一般生铁篦板 。
与此同时在应用全过程中就出現难题,因为篦板与磨球不相符合,隔仓板损坏迅速,抗压强度降低,隔仓板破裂,导致碾磨体串仓,既然停磨倒入所有磨球,开展再次配合比,停磨时间长,危害生产制造。也是鄂板与碾磨体不相符合的,如山东省GF企业Φ3 m×9 m水泥磨Ⅱ仓用Mn13的鄂板应用2~3年,而改成一般生铁鄂板仅3六个月就将其小波浪纹磨去。
3、加球计量检定不精确
水泥磨的加球要以较全方位的耗费数据统计做为基本,但是的公司因此加球只依据工作经验,或依据磨内持仓估计加,基本前提不上各种各样碾磨体配合比的合理化。以Φ2.9 m×12 m水泥磨补球状况(表2)为例:均值台时生产量为45 t/h,按球耗5%计,需生产制造6.25万t混凝土,磨机运行1 785 h,日历表日数为73 d,需加碾磨体,这类测算是创建在长期性的统计分析状况下算出的统计数据。
不一样的磨机不一样的加工工艺情况,球耗不一样,加球运行时刻表都不同样。因而,应提升生产工艺管理方面,在生产制造时会的不计量检定,不测算,不知道应补是多少,磨内缺是多少,规格型号是多少,仅仅统算,导致测算不精确。